Monday, January 20, 2014
130th Bridge
Pipelines are built to carry products from point A to point B. They are usually underground but sometimes are suspended over creeks and rivers.
This 366’ span of 12” pipeline was being held in place by 19 hangers. The hangers were weakened by corrosion from water and road salt. Further complicating matters the City of Chicago needed to do work on the bridge bearings and this required jacking the bridge up by as much as 0.750”. They turned to Midwestern Contractors and Orbital Engineering for a solution. Orbital Engineering developed a detailed bridge inspection plan and produced a report on the condition of each hanger, an analysis of the load distribution across the hangers and a set of recommendations for the repair or replacement of each hanger. In addition Orbital redesigned the hangers, making them stronger and utilizing stainless steel components to prevent future problems from corrosion.
While Orbital worked on the design and drawings, Midwestern Contractors was charged with developing the construction plan, securing a lease for access and laydown area, and securing permits from the Corp of Engineers, Illinois Department of Natural Resources, and U.S. Coast Guard.
After almost two years of work, the necessary permits were secured; the hangers were designed and fabricated; and the construction plan and sub-contractors were in place. A fall start date was anticipated but final permits did not clear until January of 2012.
Access to the site also proved to be challenging. The main span had to be accessed by barge and the approaches required scaffolding. On the West side of the bridge the scaffolding had to provide safe access for the crews but also bridge a rail spur to prevent interruptions in service to a pig iron yard. Scaffolding was required on the East side as well however there was no easy land access point. It was decided that all scaffolding would be unloaded on the West side and a portion would be barged across the river then off loaded for assembly. The scaffolding was designed to support twice the expected load of men material and equipment. The main span hangers would be placed by crews working from the man lift.
Our crews started the project on a bitterly cold, January 15th at the docks of Kindra Lake Towing, where a work barge was loaded with equipment, including, a 90 ton crane, an aerial man lift with a 70’ reach, material trailer, heated construction trailer, generator, rescue boat and rigging materials.
Midwestern Contractor’s crews began work on the 13 main span hangers while the scaffolding was being assembled. Each existing hanger was originally riveted in place over 60 years ago. These rivets had to be cut-off flush and punched-out with hydraulic jacks. Each one was difficult to remove. The redesigned hangers were fastened with structural bolts and torqued to specification. The approach hangers were to be cantilevered off of I beams placed onto the bridge structure. This was a laborious process requiring some bridge repair, drilling, alignment of the I-beams and fastening with structural bolts. A thank you is in order for Fabricating and Welding Inc. for their fine shop fabrication of the hangers and structural steel associated with this job.
Each hanger was adjusted to take its proportional load of the pipeline. On March 15th the job was completed. There was very little vibration in the Pipe line. With the new zinc rich coatings and the use of stainless steel components, the 12” pipeline should be secure for decades into the future.
Integrity work can be very unpredictable. There are many variables that can negatively affect the progress and the outcome of any project. Some are physical like snow and wind; others are abstract like the words on a permit. In every case a competent contractor should build relationships with his customer, engineers and regulators. The result will be a successful project that all parties can be proud of that is completed on time.
CASE STUDY GALLERY
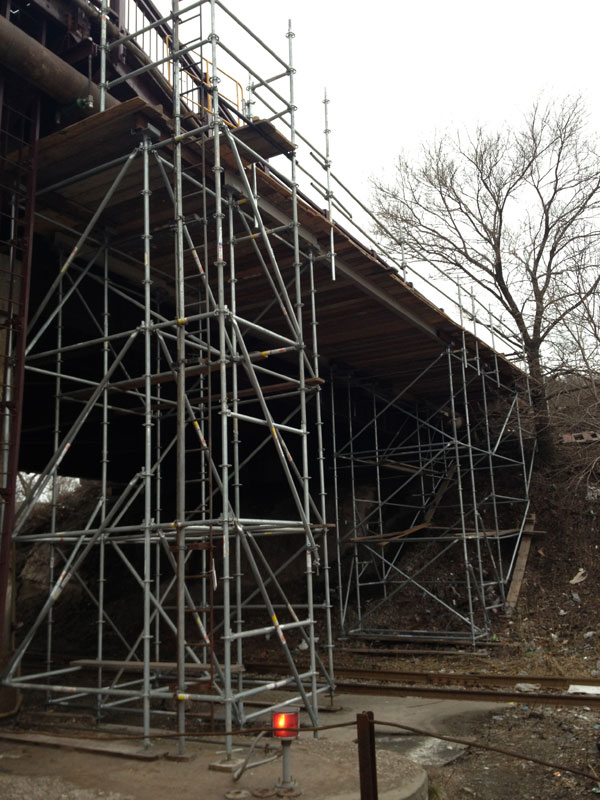
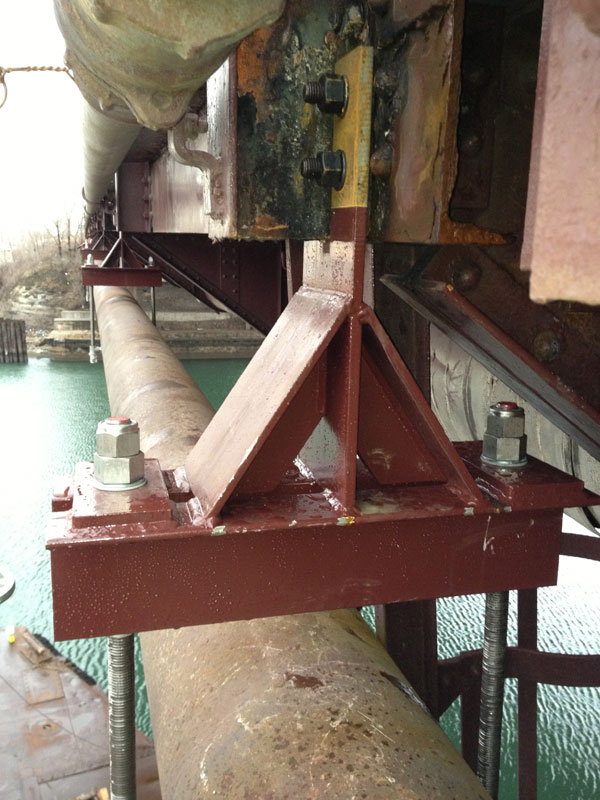
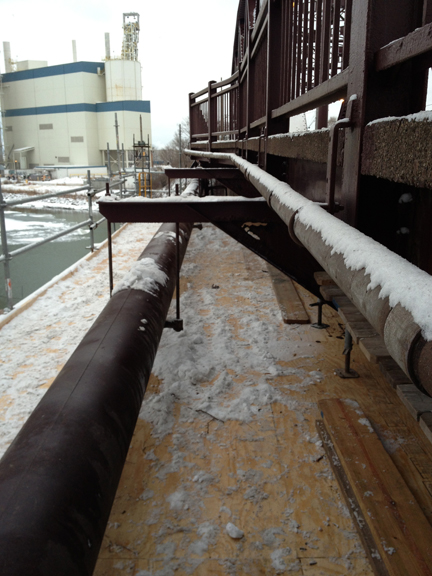
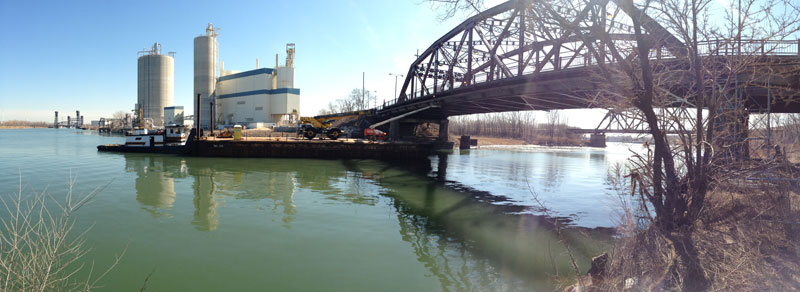
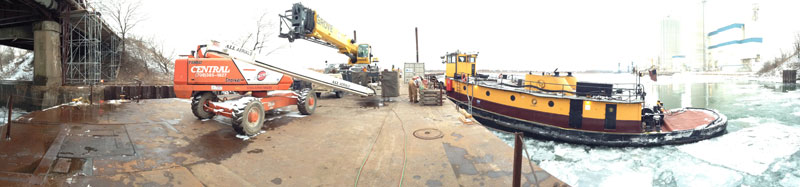
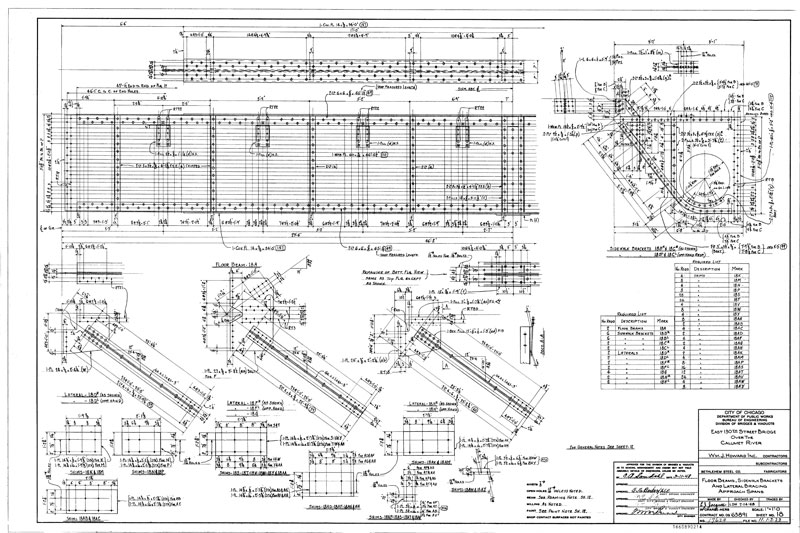
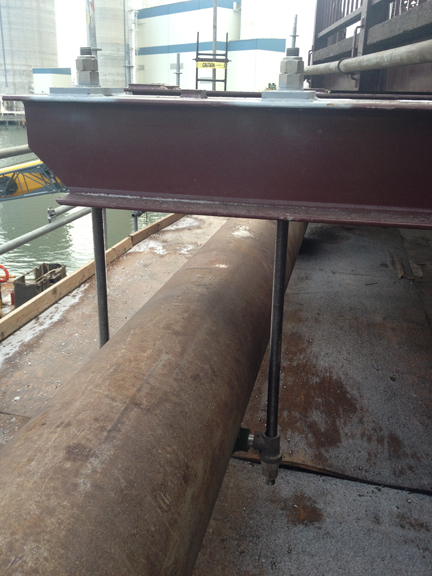